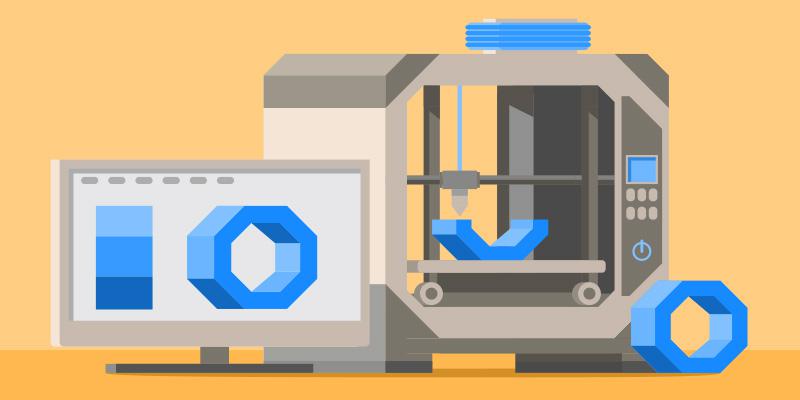
Additive Manufacturing? What A.M. I talking about?
What is additive manufacturing?
The image that comes to mind when most of us think of manufacturing is not one of additive manufacturing but rather subtractive manufacturing. This is the traditional method of making things that we are all very familiar with, which involves taking away material to make a part or product.
Think of a chair: you have pieces of wood that you cut and whittle down into legs and maybe arms, there’s a large roll of fabric and a chunk of foam that you cut the upholstery and padding out of and then you put it all together. You subtract the chair shaped pattern out of the materials and assemble it.
Now, there’s a whole new way of doing things. Additive manufacturing is the opposite of subtractive manufacturing because instead of cutting parts out of a larger whole, the material is created in the shape you need it in, right from the beginning.
We chatted with our partner Vetted Tech, located in Syracuse, NY, to learn more about additive manufacturing, and now we’re sharing our knowledge with you! To learn more about Vetted Tech check out our video: Meet Vetted Tech.
How it works:
Additive manufacturing relies on CAD, or computer aided design. This is a type of computer program that allows engineers to create their design digitally and then the program slices that design into thin layers. Next, a machine, such as a 3D printer, is able to build the design up, forming it layer by layer, allowing for more flexibility in the design.
3D printing is the classic example of additive manufacturing. You can see how the material is added during the 3D printing process, since the nozzle squeezes the material out like a toothpaste tube only where the material is meant to be.
Some methods of additive manufacturing don’t squeeze material out of a tube but rather use heat to solidify or cure powdered materials such as plastic, metal, or other polymers. This process starts with a thin layer of powdered [insert material here] - additive manufacturing technologies are compatible with a very large variety of materials.
Next, a laser heats the powder, melting it together and creating the first layer of the design. Then, another layer is spread over the first as that first layer descends into the machine so that the top, working layer is always on the same plane for the laser. The laser does its thang again, and so on and so forth until the whole design has been crafted. At the very end, the object is raised back up and the powder falls away, revealing the product.
If you’re more of a visual learner, and this description just isn’t doing it for you, check out this video from GE.
What are the implications for the manufacturing industry?
These additive manufacturing techniques can eliminate some of the obstacles of traditional, subtractive manufacturing.
For example, additive manufacturing allows for much more intricate shapes, and stronger ones too. Think of a simple metal chain: each link needs to be fused at some juncture in order to connect them together and that juncture then becomes a point of weakness. With additive manufacturing, however, the whole link can be made already intertwined with the others. This is because of the layer-by-layer nature of additive manufacturing.
Additionally, additive manufacturing allows for flexibility while working with a lot of materials that traditionally are not very easy to work with. With metallic powders, metal objects can be created without having to bend or mold metal into tricky shapes.
Types of Additive Manufacturing
Laying out the alphabet soup of all the different types of additive manufacturing.
Powder Bed Fusion (PBF) –
This is the name for processes like the powder and laser process described above and other techniques like it including:
DMLM |
Direct Metal Laser Melting |
DMLS |
Direct Metal Laser Sintering |
EBM |
Electron Beam Melting |
SHS |
Selective Heat Sintering |
SLS |
Selective Laser Sintering |
Material Extrusion –
This process is like the 3D printing process described above; material quite literally extrudes from a nozzle as the 3D printer lays it down. Like the PBF method, the design is slowly lowered so that the laser, moving on a horizontal plane can stay in the same vertical positioning as it lays down each successive layer.
Other Types of Additive Manufacturing –
Directed Energy Deposition (DED) |
The process of directed energy deposition (DED) is similar to material extrusion, although it can be used with a wider variety of materials, including polymers, ceramics and metals. An electron beam gun or laser mounted on a four- or five-axis arm melts either wire or filament feedstock or powder. |
Material Jetting |
With material jetting, a print head moves back and forth, much like the head on a 2D inkjet printer. However, it typically moves on x-, y- and z-axes to create 3D objects. Layers harden as they cool or are cured by ultraviolet light. |
Binder Jetting |
The binder jetting process is similar to material jetting, except that the print head lays down alternate layers of powdered material and a liquid binder. |
Sheet Lamination |
Laminated object manufacturing (LOM) and ultrasonic additive manufacturing (UAM) are two sheet lamination methods. LOM uses alternate layers of paper and adhesive, while UAM employs thin metal sheets conjoined through ultrasonic welding. LOM excels at creating objects ideal for visual or aesthetic modeling. UAM is a relatively low-temperature, low-energy process used with various metals, including titanium, stainless steel and aluminum. |
Vat Polymerization |
With vat photopolymerization, an object is created in a vat of a liquid resin photopolymer. A process called photopolymerization cures each microfine resin layer using ultraviolet (UV) light precisely directed by mirrors. |
Source: GE
How is this technology being applied?
Because of the flexible nature of additive manufacturing, it is often used to prototype parts and products. For Vetted Tech and companies like it, this rapid prototyping is one of the most common uses for their additive manufacturing capabilities.
This is because, generally, additive manufacturing is not currently a mass production method, though there is a lot of potential for those applications in the future. Right now, it is used to create small batches with high variation between each lot.
This allows product developers to design a product, manufacture it quickly, test it for design flaws, and edit their design to start the process again. Once they have the prototype worked out, they can invest in the tooling and infrastructure needed to mass produce it using traditional, subtractive manufacturing.
Similarly, in the defense industry, additive manufacturing is often used to produce spare or obsolete parts for maintenance. This cuts down on the inventory expenses of having spare parts constantly on hand, as well as the logistics expenses of procuring and shipping those parts around the globe.
Even when parts are shipped around the globe, additive manufacturing greatly reduces the weights of the material which would cut down on logistics costs. One reason for the reduction in weight is that, like the metal chain example, parts can be made already connected thereby reducing the number of parts used in the final product and, consequentially, its weight. There is much less need to weld or bolt parts together.
This is a major benefit in the aerospace industry as well, where the approximately 30 3D printed parts that were certified for flight in 2020 replaced over 50 traditionally manufactured parts (TCT). Additionally, the wide array of materials available with 3D printing make it especially good at manufacturing parts for heat and fluid management on aircraft.
Much of what makes additive manufacturing so good at rapid prototyping also makes it a great method for producing highly customized products. In defense and aerospace, this may mean developing casings for drones or other flying objects that are customized to a specific mission or environment.
This customization is a major reason additive manufacturing has taken off in the medical field. CAD has made it possible to use patient scans to design highly personalized devices. Again, the small batch sizes with high variation between each patient’s specifications makes additive manufacturing ideal for the medical industry.
Additive manufacturing is allowing manufacturers to make stronger, more intricate, and more specialized parts. As the technology becomes more widely available, these techniques will continue to grow in popularity and their use for mass production will become more feasible. Additive manufacturing continues to be an excellent solution for product development and customized products especially in the early-adopting defense, aerospace, and medical fields.

Catherine McConnell
Marketing InternFormer marketing intern at Perdix Software, Catherine McConnell is a SUNY Brockport Graduate with a BS in Dance and Finance. Her previous work experience includes Market Research Consulting through Entrepreneurs EDGE, and a marketing internship at ImpromptMe, Ltd. Currently, Catherine is employed as Project Coordinator at Transperfect.
With her dual passions for creativity and analysis, Catherine has found marketing to be the perfect combination of the two. Having grown up dancing, Catherine was able to learn communication, artistic skills, and self-promotion from a young age and is pleased to be able to put those skills to use promoting small businesses and economic development. In her free time, Catherine enjoys dancing, cooking, and listening to podcasts.